Comparing cleanroom solutions: Which suits your requirements?
Clean rooms are essential when it comes to manufacturing and developing sensitive products. However, not every application requires a permanently installed clean room. Sometimes a local solution such as a laminar flow box is enough, while in other cases a modular cleanroom cabin is the better choice. This article shows the most important differences between the various variants — and why the right selection is crucial for efficiency and quality.
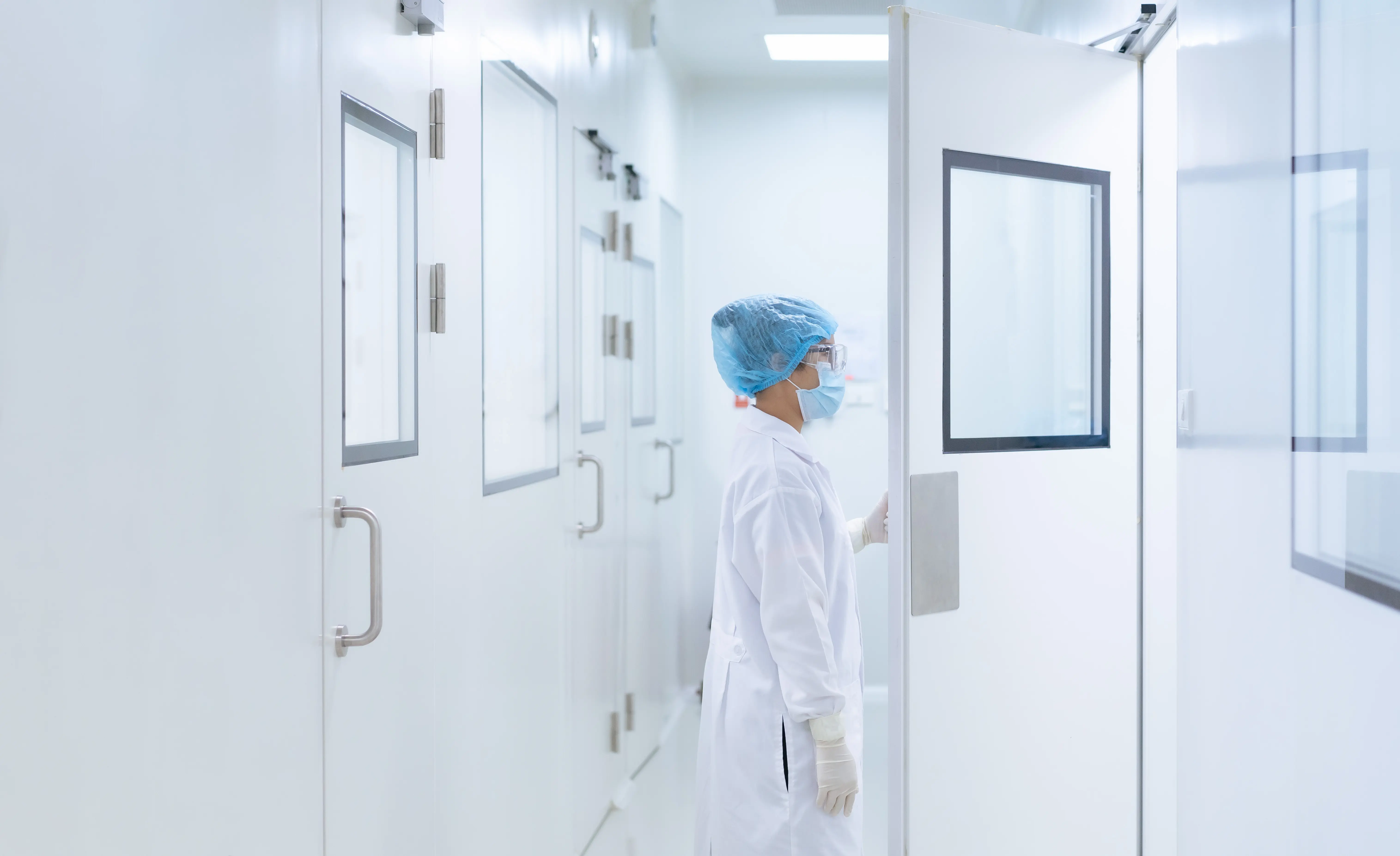
1. Permanently installed clean rooms: the standard for maximum control
Fixed clean rooms offer unparalleled control and efficiency. They are precisely tailored to the requirements of purity, air exchange rates and room climate, which makes them indispensable for complex production processes.
Especially in semiconductor production, where ISO Class 5 clean rooms are required, they guarantee a maximum particle concentration of 3,520 particles ≥0.5 µm per cubic meter. Even stricter classes such as ISO 3 are easier to implement in permanently installed clean rooms, as their sophisticated ventilation systems usually extend over several floors and must be carefully planned for new buildings. It is often difficult to install such systems retrospectively.
Large cleanroom projects, which cover several hundred square meters, pay for themselves through increased energy efficiency and optimized production conditions. In addition to improving production quality, the regulation of other air parameters such as temperature and humidity plays a major role. For applications that require ISO Class 4 or better clean rooms, ULPA Class 15 or 16 filters are used as they meet even the strictest cleanliness requirements. However, modern HEPA H14 filters remain an essential standard for many projects, as they remove up to 99.995% of all particles ≥0.3 µm and thus ensure high purity standards.
.webp)
2. Cleanroom cabins: flexibility for growing requirements
Modular cleanroom cabins are the ideal solution for companies that need a quick and adaptable cleanroom solution. They can be installed directly in existing production halls and even dirty environments and can be expanded or adapted as required. In addition, they allow access controls to be integrated and offer higher cleanliness than cleanroom tents in a relatively protected environment, making them particularly versatile.
An example from electronics manufacturing shows how effective cleanroom cabins can be. They offer ISO 5 conditions that are sufficient for the assembly of sensitive microchips without the high energy and investment costs of a permanently installed clean room.
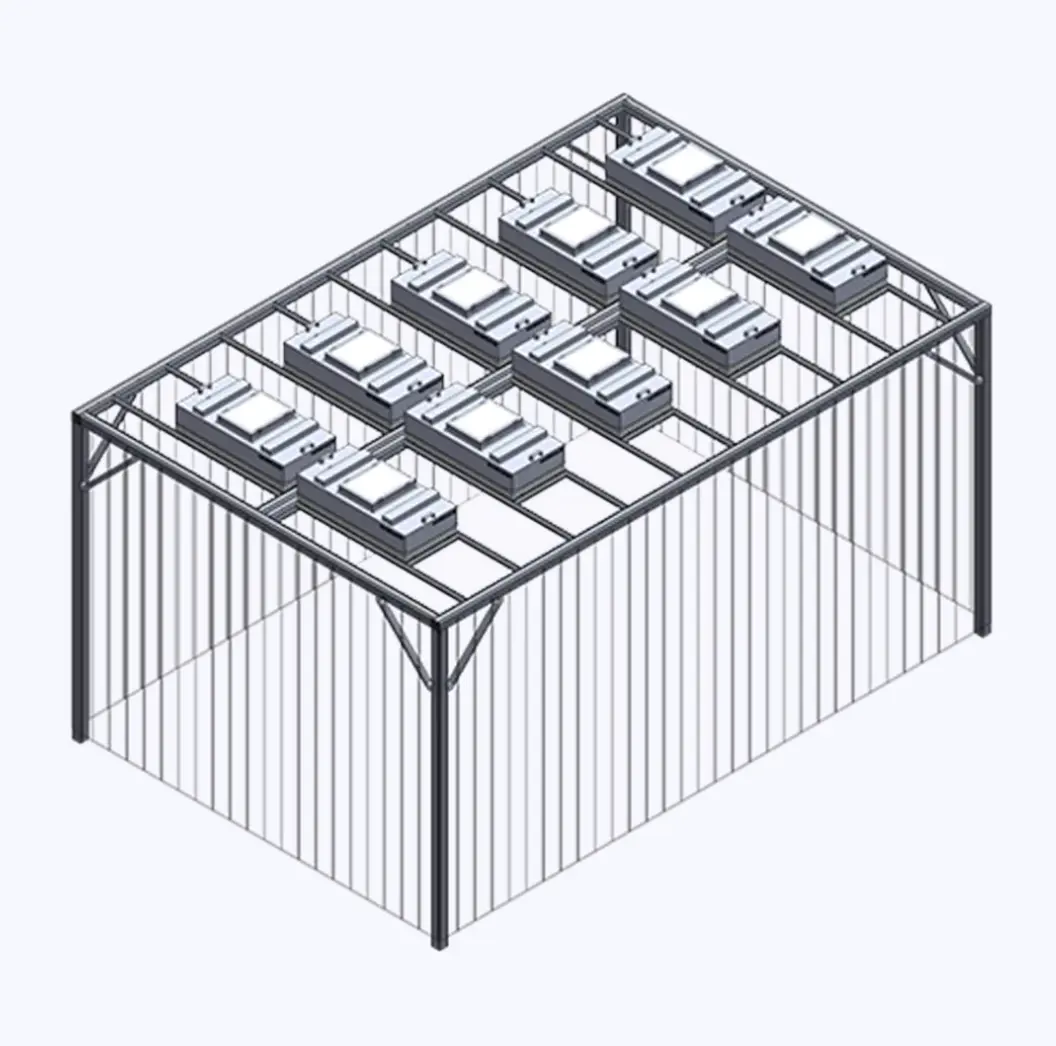
3. Cleanroom tents: Quick and cost-effective
When flexibility and costs play a bigger role, cleanroom tents offer a practical solution. They are made from lightweight, flexible materials and can be quickly assembled or dismantled as required.
While they are often used for applications where ISO 8 conditions are sufficient, a purity of up to ISO 5 can even be achieved through the use of a sophisticated lock concept.
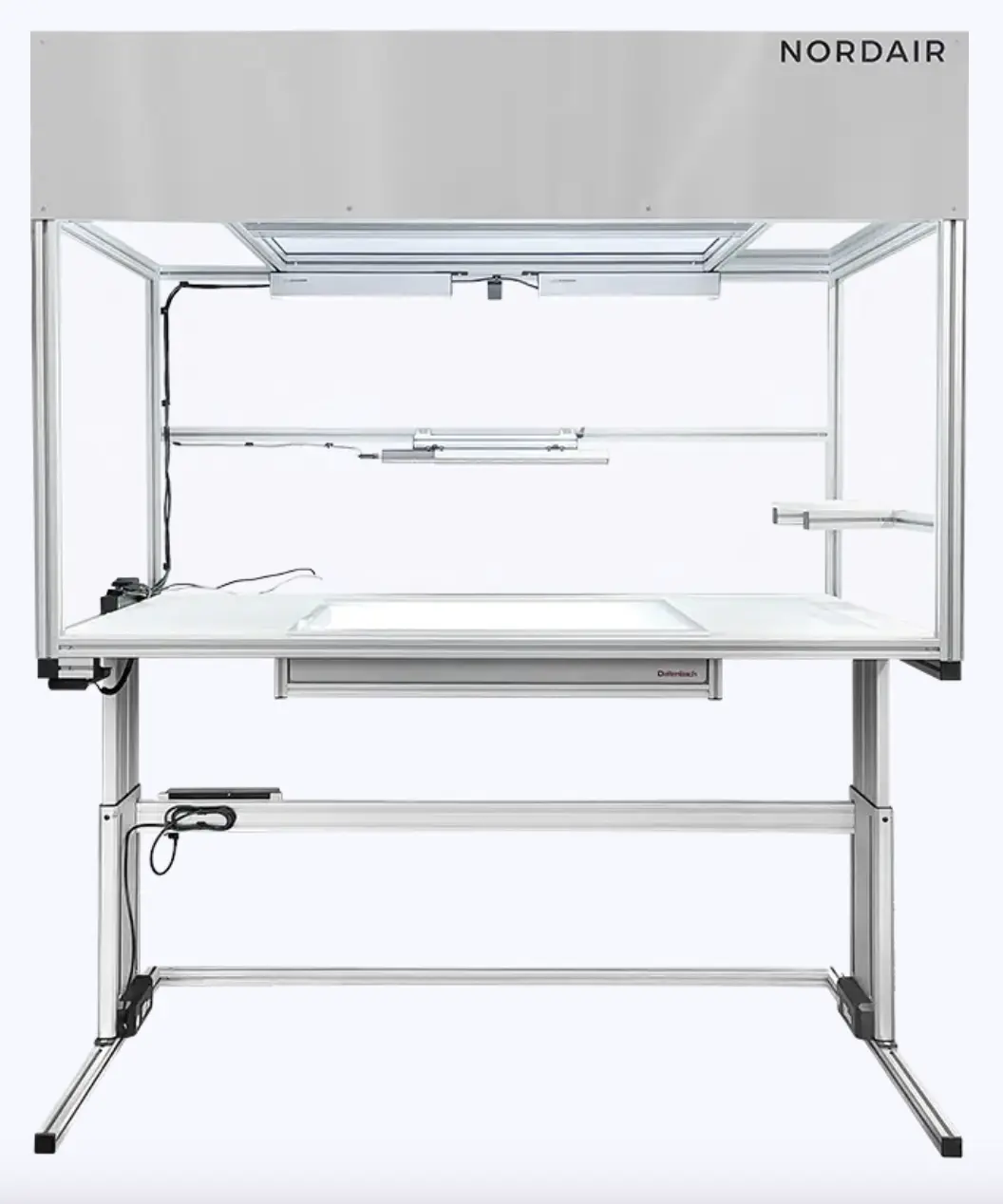
4. Laminar flow boxes: purity in small format
Laminar flow boxes create locally controlled cleanroom conditions. Through unidirectional air flow, particles are immediately removed, which enables a sterile working environment.
One common area of application is laser technology, where laminar flow boxes are used to process or clean highly sensitive optics or components in a dust-free environment. These boxes guarantee ISO 5 conditions without the energy consumption of a complete clean room.
The right solution for your needs
The choice of the right cleanroom solution depends on the requirements of your production. Permanently installed clean rooms offer maximum control, but have very high initial investments and offer few development opportunities. Meanwhile, modular cabins and in particular cleanroom tents also offer cleanroom conditions in accordance with ISO 5 and are significantly more flexible and cheaper. Laminar flow boxes are ideal for applications that only have locally limited cleanliness requirements.
Source citations
- ISO 14644-1:2015, clean rooms and associated clean room areas — Classification of air purity by particle concentration.
- Ljungqvist B., Reinmuller B. (2020), People as a Contamination Source in Pharmaceutical Cleanrooms. DOI: 10.5731/pdajpst.2020.012054.
- Whyte W., Ward S., Agricola K. (2018), Ventilation Effectiveness in Cleanrooms, European Journal of Parenteral and Pharmaceutical Sciences, 23 (4).
- Perry, J., Agui, J., & Vijayakumar, R. (2016). Removal of submicron and nanoparticle contaminants by HEPA-rated media filters and packed beds of granular materials. Journal of Aerosol Science.